putting an end to end-of-life
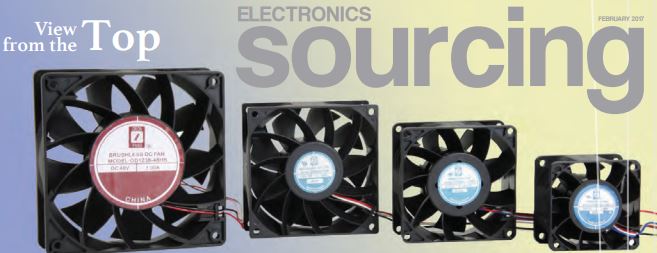
Obsolescence, or end of life, has been a hot topic of discussion in recent years. As a result, we all know that these critical events can present significant procurement challenges, including continuity of manufacturing, quality, cost management and support: not to mention the future field maintenance costs. There are typically constraints when selecting a device replacement based on the original system design as well as customer requirements such as cost and time, or functional and environmental parameters. There may also be issues with industry certifications, matching components for identical drop-in capability and supply issues for the immediate and life of the product time frames.
We often discuss that when EOL events occur, collaboration across the supply chain can solve the procurement, replacement or design challenges. This is true. Partnership between end-product manufacturers, original component manufacturers and component distributors can lead to appropriate short-term supply chain options for the device going EOL. Distribution partners may also be in tune with retrofit and replacement solutions. We read about components having shorter life cycles and about how discontinuing the production of materials, components and devices is a part of everyday life in manufacturing. The industry knows that every material, product and technology has a life cycle. It is therefore only a matter of time before the manufacturer needs to make way for the next-generation part or, as product demand falls to smaller volumes, it becomes unprofitable to continue producing a particular part or series.
We learn about taking steps to minimize the impact of the inevitable product discontinuance notice and that original equipment manufacturers need to strategically plan for an EOL event in order to keep their own manufacturing lines up and running.
We know too that counterfeiting is a problem within the electronics world that is only exacerbated by EOL events. Today, even less-sophisticated, lower cost parts are being counterfeited. Procurement professionals understand that to ensure product quality, working with an authorized supplier with a proven record of product authenticity and traceability to the original manufacturer is necessary.
Unfortunately, what we don’t talk about is ending end-of-life. The most suitable solution for OEMs is to partner with an original component manufacturer that has a no obsolescence policy. Component manufacturers that have made this pledge to their customers are few and far between, but some have made a commitment that no matter what the volume for a particular product, they will not impose an EOL event on their customers.
There are many pain points in the design and manufacturing process. End of life announcements do not have to be another point of concern.